CONCRETE 3D-PRINTING
//date_ august 2020
//location_ sdu odense, denmark
//methods_ robotic 3D-printing
//tutors_ prof. dr. roberto naboni, anja kunic , luca breseghello, sandro sanin
Robotic Concrete 3D Printing challenges the conventional design standards of concrete construction by exploring the potentials and flexibility of Direct Concrete 3D Printing. Combining computational design logics, structural performance optimization and material experiments, the project aims to push the boundaries of what can be built in concrete and to reduce costs, time and labour for a more sustainable construction.
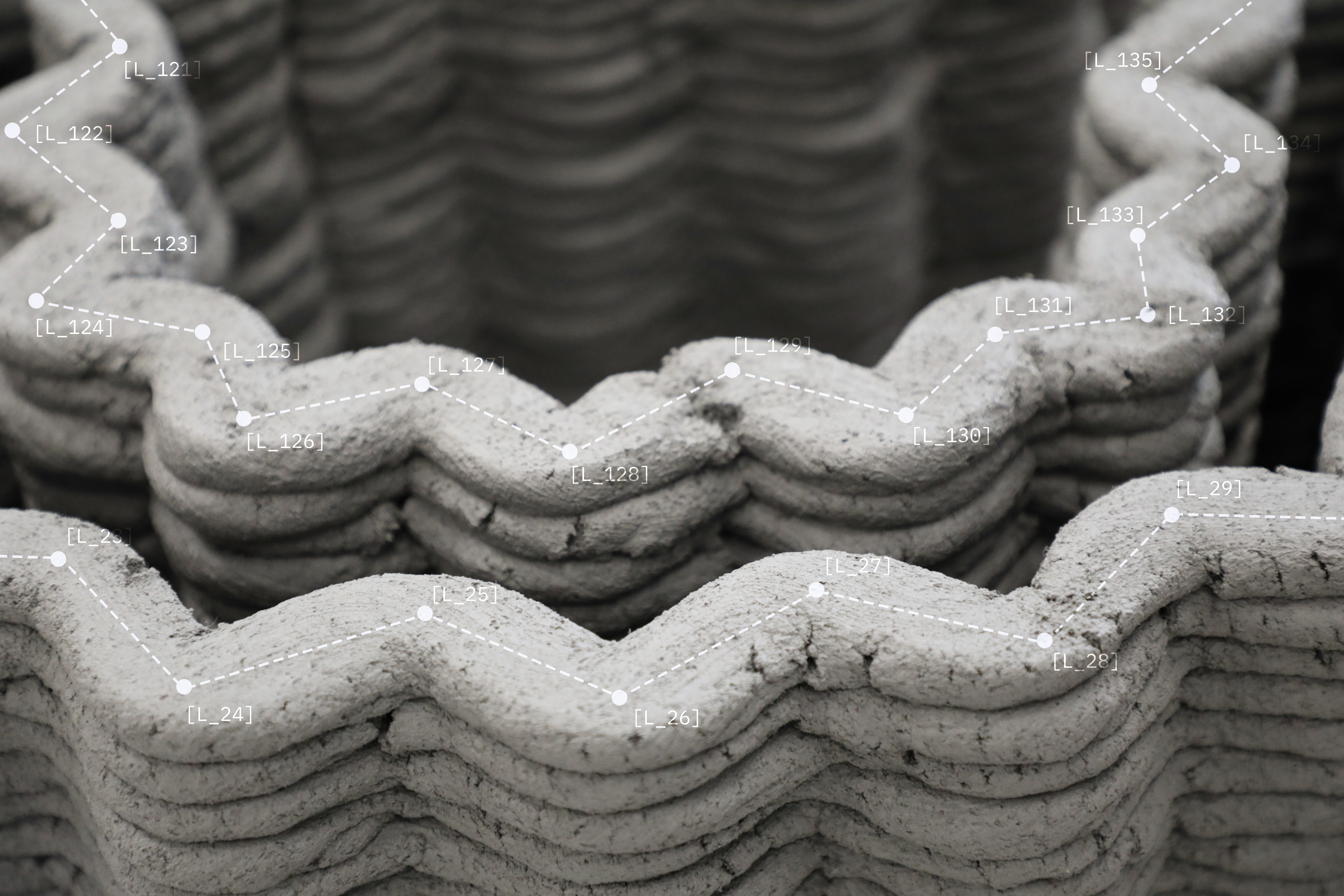
//3d-printed wall element
This project was conducted by the SDU Create in their 2020 Summer School format. In collaboration with partners from concrete industry and with 20 international students the aim of this intense 2-week-workshop was to challenge construction standards at two intertwined scales: a series of patterns are tested on a standard column design as a mean of improving the structural performance of concrete elements, and then applied to a non-standard highly-complex large-scale design that proves the design freedom and customization possibility of the technology.
//Objective 1 Increasing column height by strategically adjusting toolpath speed to apply material where it is needed.
//Objective 2 Gaining mechanical stability by implementing internal ribbing structures.
//Objective 3 Increasing stiffness of the column by incorporating oscillating reinforcement patterns.
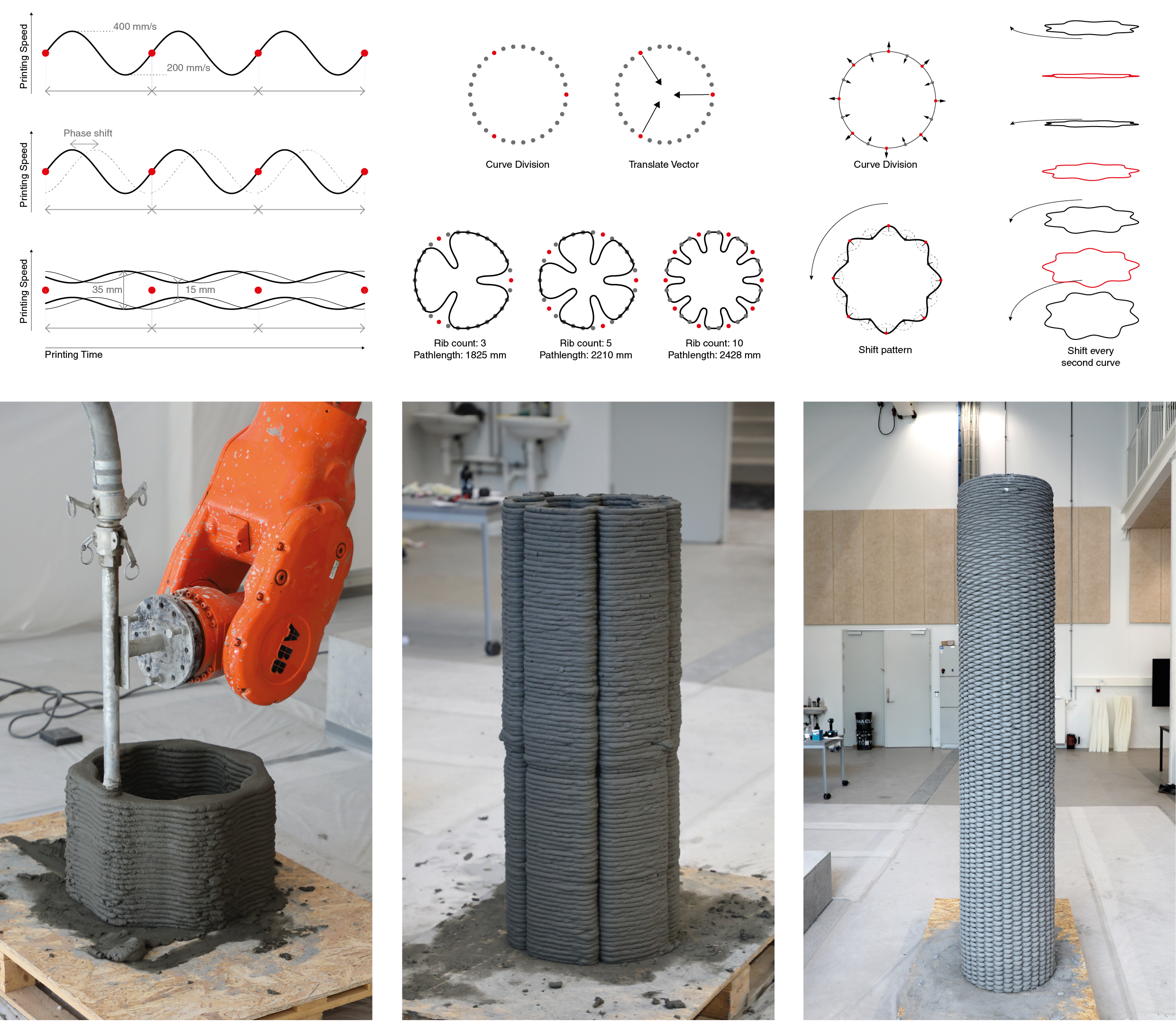
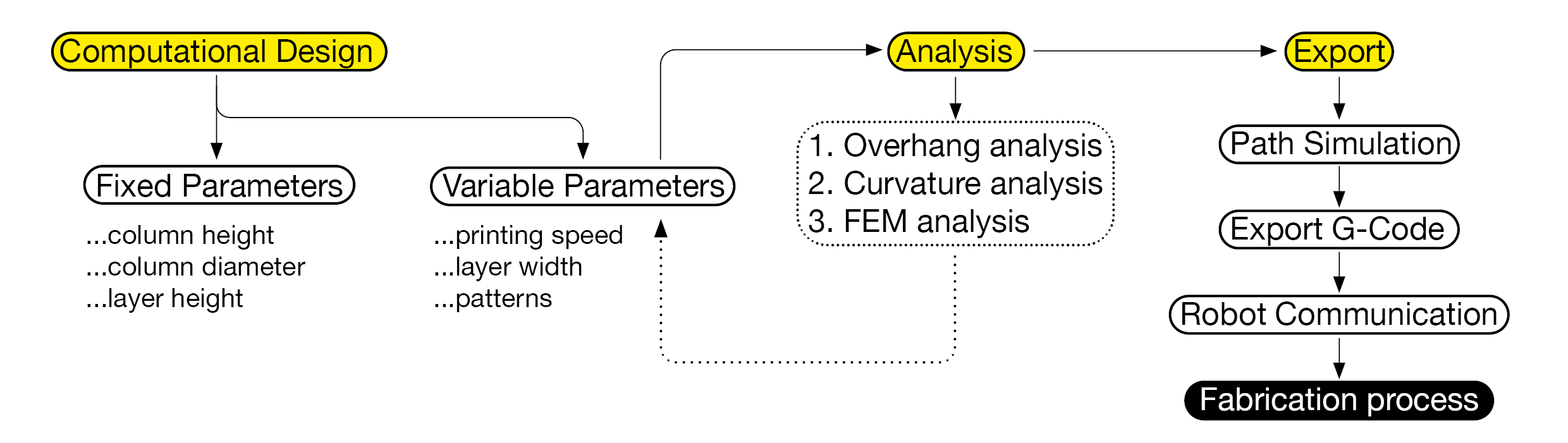
//digital workflow
The computational pipeline incorporates fabrication parameters such as printing speed, nozzle diameter, extrusion rate and performs structural analysis of the designed column to ensure fabricability and stability of the designed structure. After the geometry generation and slicing a 6-axis industrial robot was employed to deposit a fine-grained, fiber-reinforced concrete mixture layer by layer.

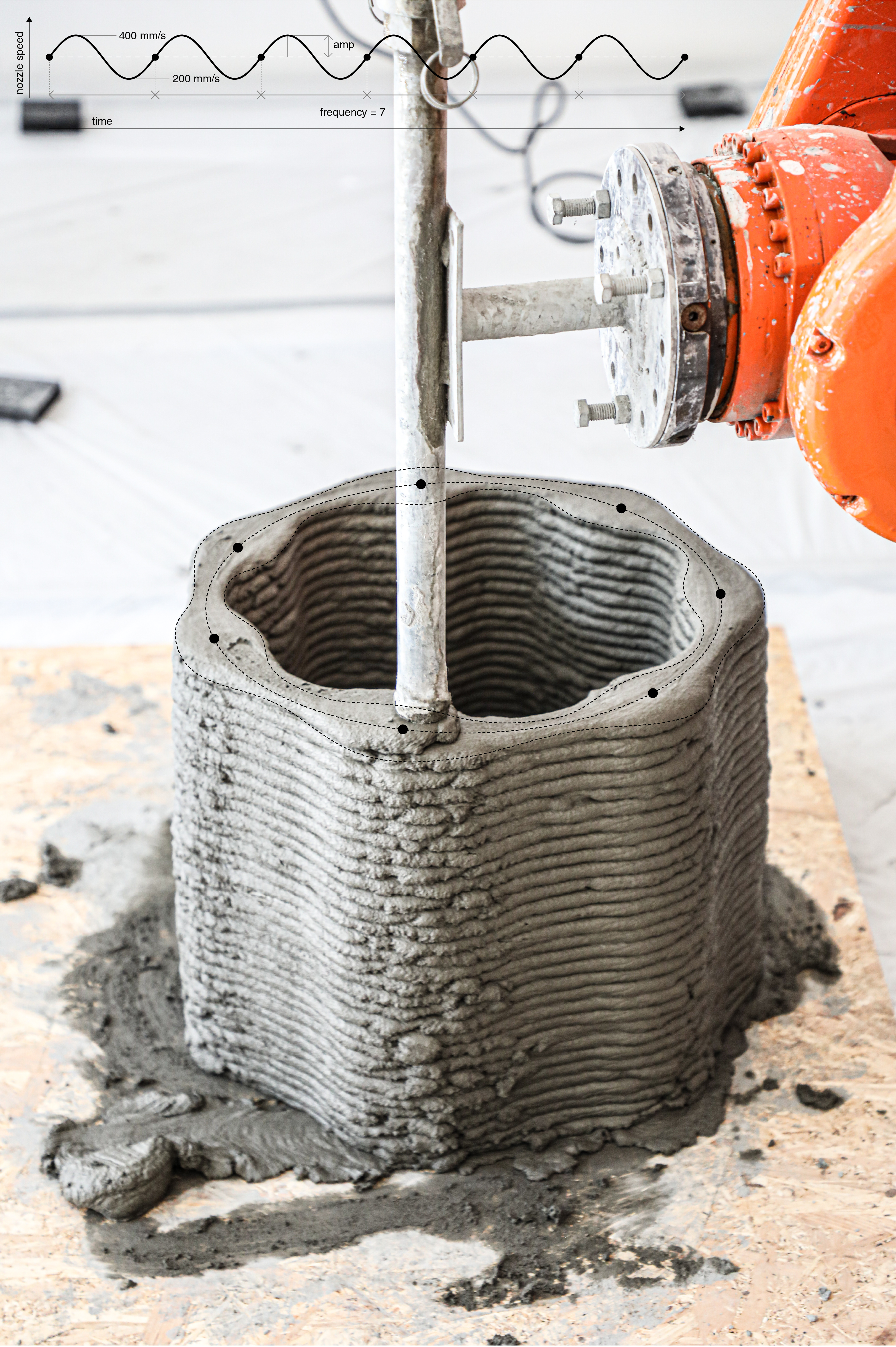
//printing process + speed manipulation
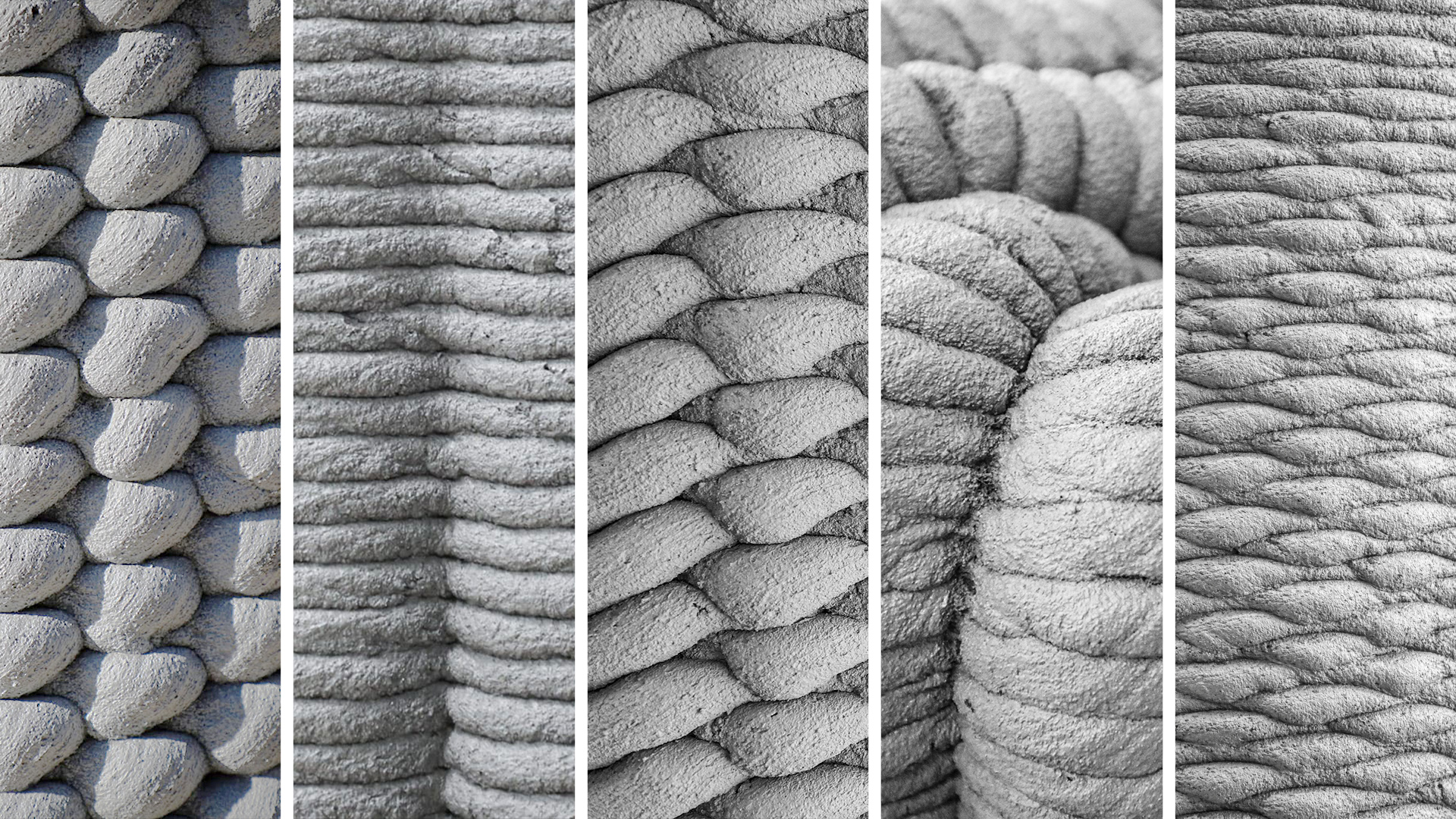
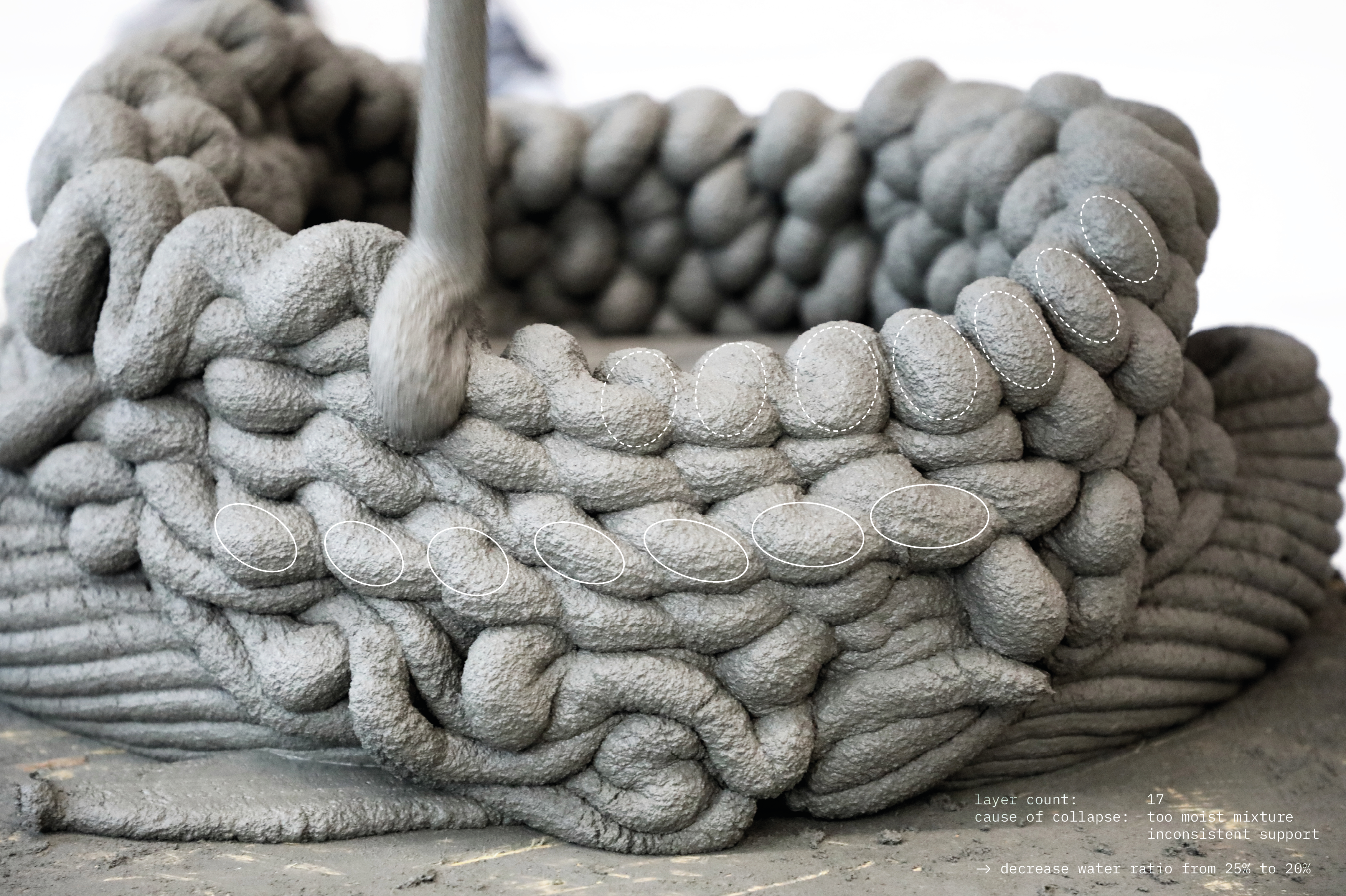
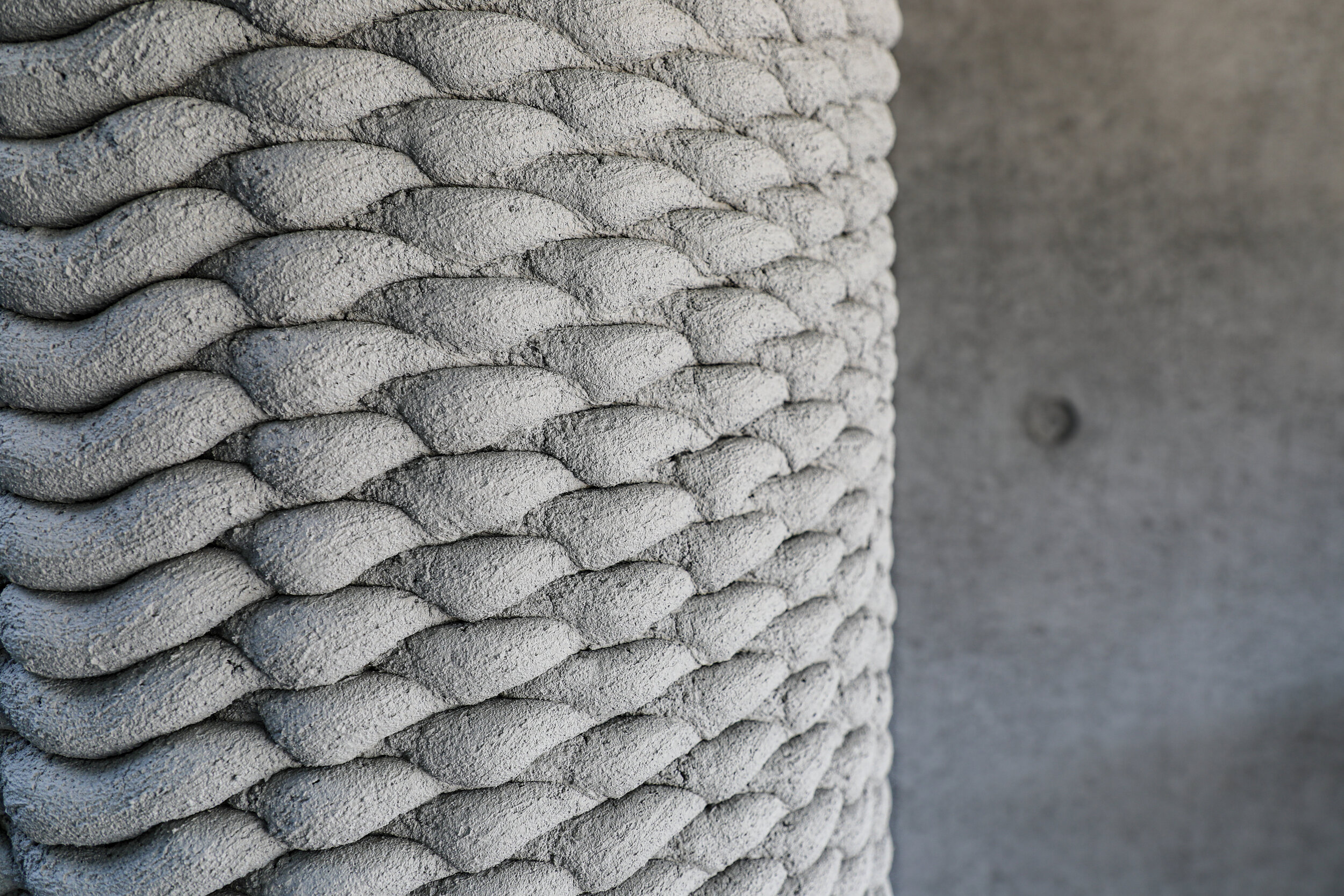
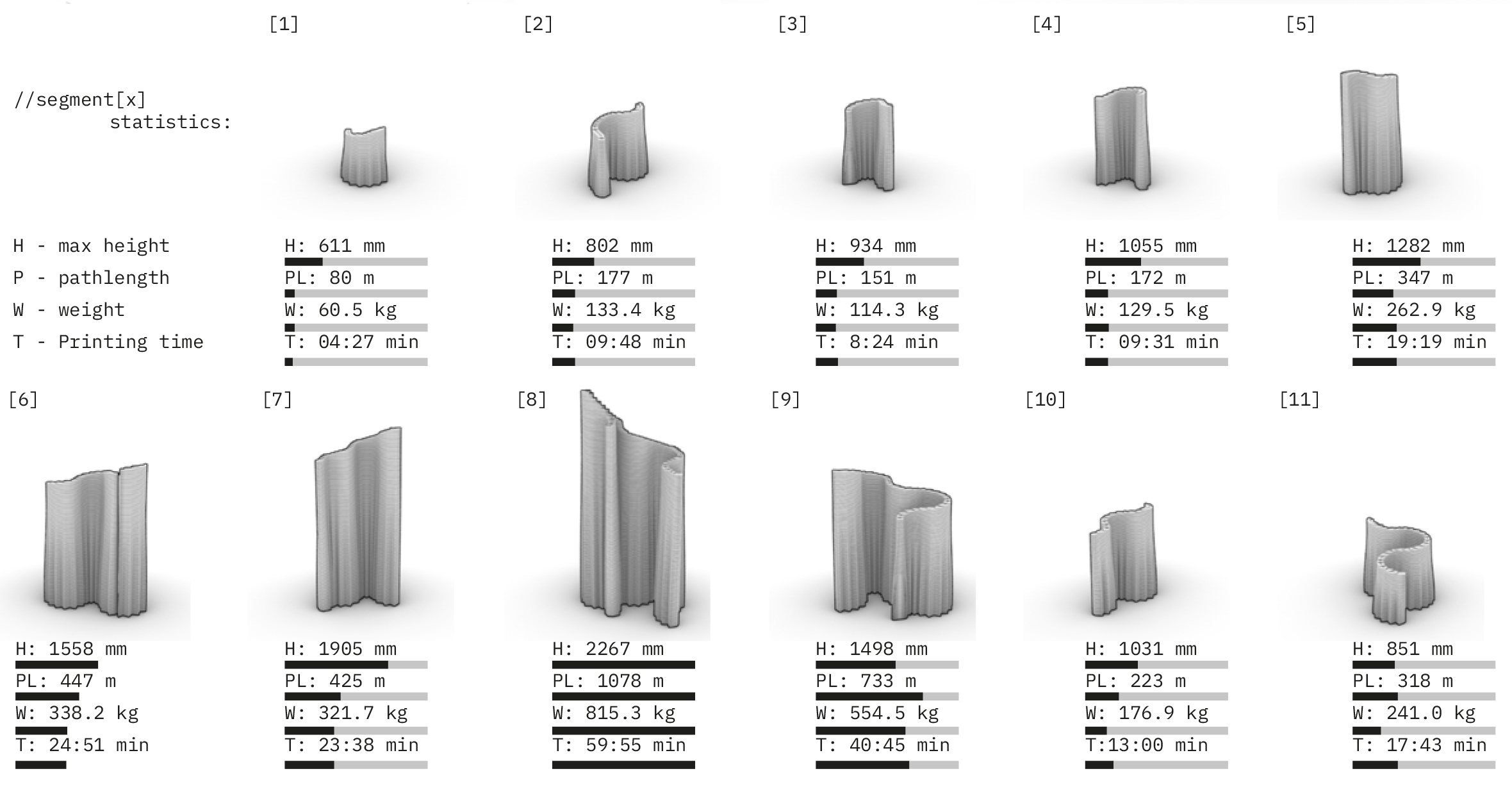



//credits
//CREATE Group_ Led by Asst. Prof. Dr. Roberto Naboni
//industry partner_ Hyperion Robotics
//students_ Ilyas Abdirashid Ahmed, Kawtar Al Akel, Peter Christian Kjær Balle, Fabian Eidner, Styrmir Gislason, Robert Tøste Lomholdt Jespersen, Camilla Juul Johansen, Anders Klitgaard Klausen, Dominika Aleksandra Krolikowska, Mads Friborg Nielsen, Mads Køhler Persson, Søren Rasmussen, Kasper Lund Rasmussen, Lasse Weyergang Rahbek, Helena Schenavsky, Martyna Skóra, Troels Sperling, Valdemar Brandt Thygesen, Mads Sørensen, Simon Andreasen Andreasen, Philip James Douglas
//concrete material_ Weber Saint-Gobain Denmark
//concrete admixtures_ Fosroc Denark
//polypropylene fibres_ Danish Fibers
//CREATE Group_ Led by Asst. Prof. Dr. Roberto Naboni
//industry partner_ Hyperion Robotics
//students_ Ilyas Abdirashid Ahmed, Kawtar Al Akel, Peter Christian Kjær Balle, Fabian Eidner, Styrmir Gislason, Robert Tøste Lomholdt Jespersen, Camilla Juul Johansen, Anders Klitgaard Klausen, Dominika Aleksandra Krolikowska, Mads Friborg Nielsen, Mads Køhler Persson, Søren Rasmussen, Kasper Lund Rasmussen, Lasse Weyergang Rahbek, Helena Schenavsky, Martyna Skóra, Troels Sperling, Valdemar Brandt Thygesen, Mads Sørensen, Simon Andreasen Andreasen, Philip James Douglas
//concrete material_ Weber Saint-Gobain Denmark
//concrete admixtures_ Fosroc Denark
//polypropylene fibres_ Danish Fibers