PNEUMATICA
//date_ october 2023
//location_ Autodesk Technology Center / Harvard Kirkland Gallery, Boston
//collaborator_ Oliver Moldow
//advisors_ Mathias Maierhofer, Tobias Schwinn
//methods_ Augmented Reality
Inspired by early DIY inflatable pioneers such as Ant Farm, Haus-Rucker-Co, and Archigram, this project explores how democratized space-making can evolve using tools and materials available in the 21st century. This research develops an intuitive design-to-fabrication workflow for inflatable construction, encouraging user participation in shaping our built environment. To achieve this, established patterning and manufacturing logics of current pneumatic production must be reevaluated and reimagined through the lens of user involvement.

Unlike current inflatable or pneumatic production methods, which rely heavily on specialized spaces and tools and result in hundreds of one-of-a-kind components, this research takes a different approach -- How can fabrication space and the number of individual parts be minimized, and the manufacturing enabled with everyday household tools?
To address this, a fabrication-oriented patterning logic was developed, discretizing complex 3D geometries into a set of 10 developable units. Each unit is a permutation of the folding pattern used for painter’s tarps and Mylar safety blankets. By cutting the material in its folded state, these units can be produced en masse within seconds.
HDPE, taken from painter's tarps, and Mylar, taken from emergency blankets, have a relatively low embodied carbon compared to conventionally used materials in pneumatic construction due to their extreme thinness. However, they lack durability and are prone to cracks, making them unsuitable for high-pressure pneumatics but ideal for air-supported, low-pressure systems. They excel in affordability and manufacturability, allowing for ad-hoc fabrication with portable tools. Their lightweight nature enables rapid inflation using minimal airflow from a standard desk fan, requiring only low operational energy.

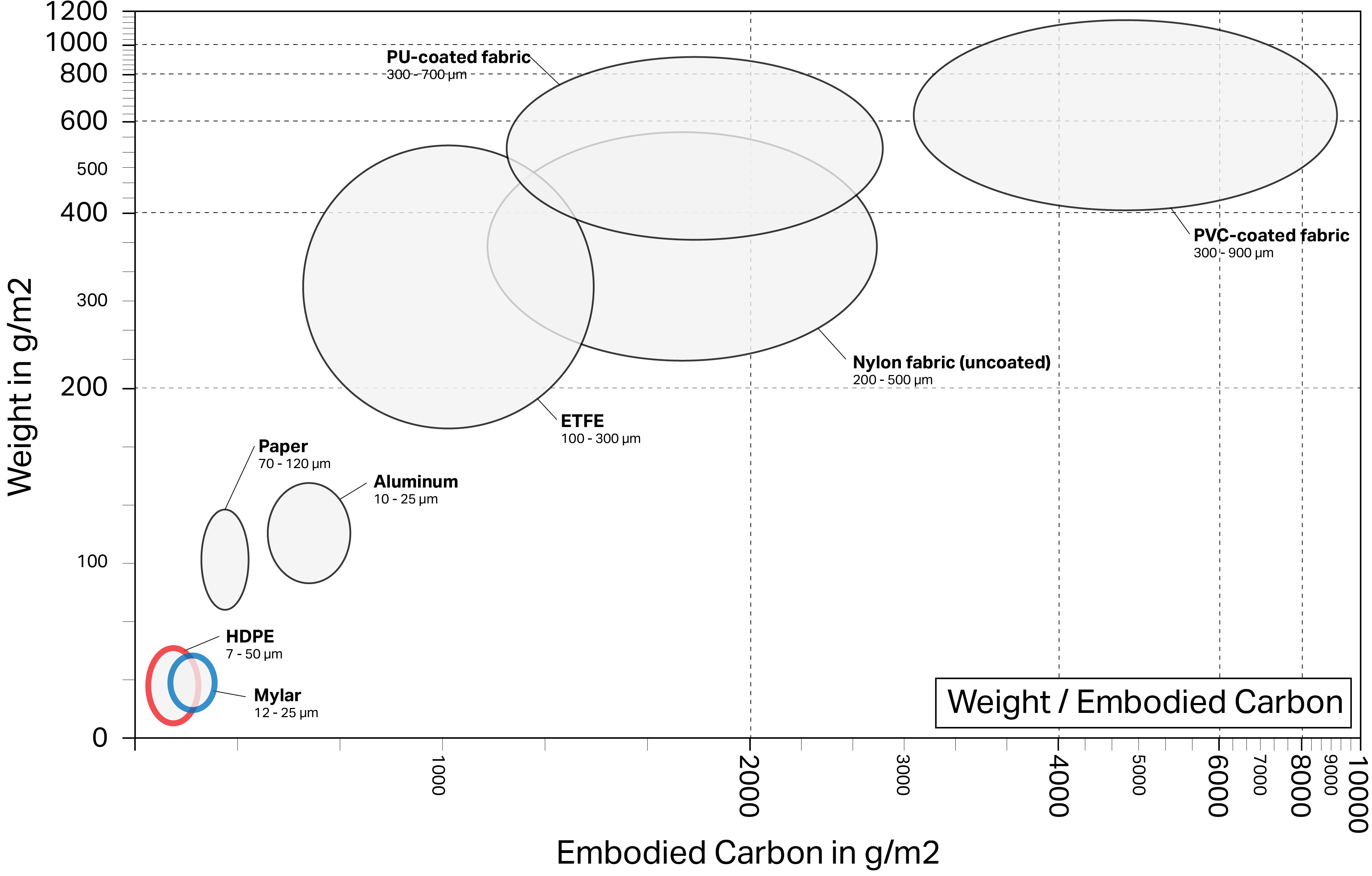
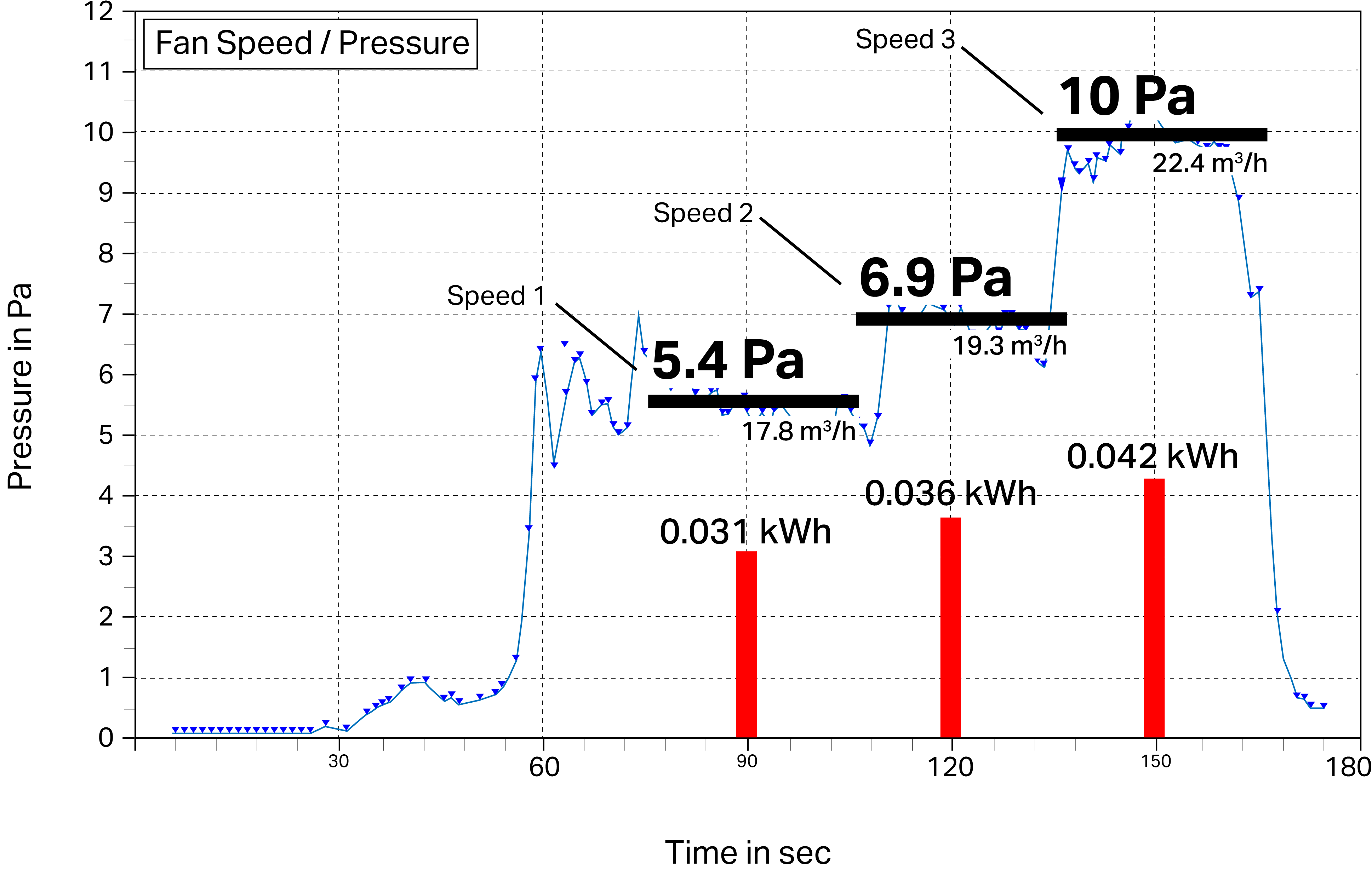

To understand the impact of the different material properties of HDPE and Mylar on the indoor climate, a set of four experiments was conducted. A triplet of insufflated, occupiable cells was fabricated (HDPE with taped seams, HDPE with buttoned seams, and Mylar) and placed in four different scenarios (indoor occupied, indoor unoccupied, outdoor shade, and outdoor sun). Both the indoor temperature and humidity were monitored over a 2-hour period during early afternoon.
![]()
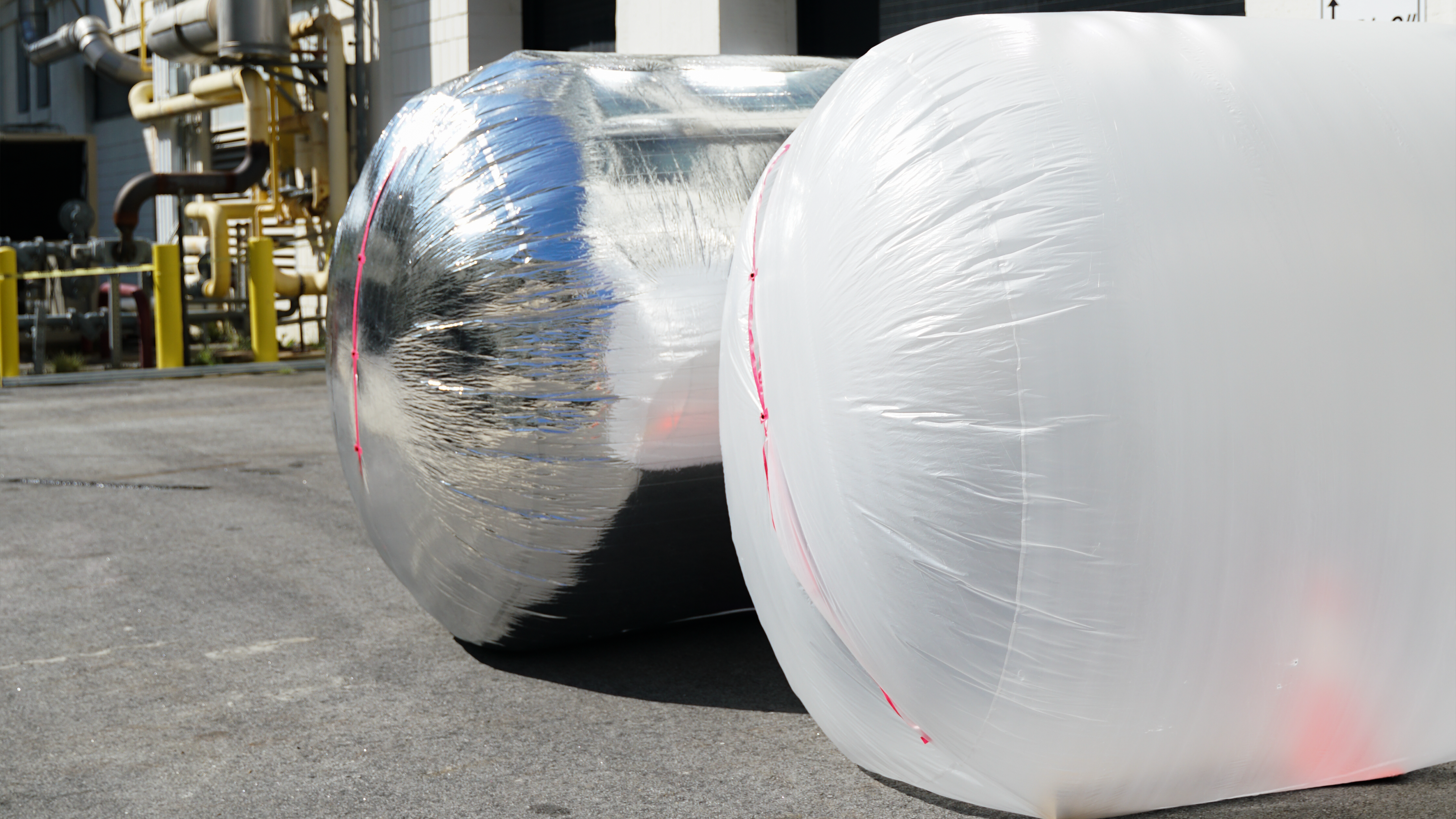
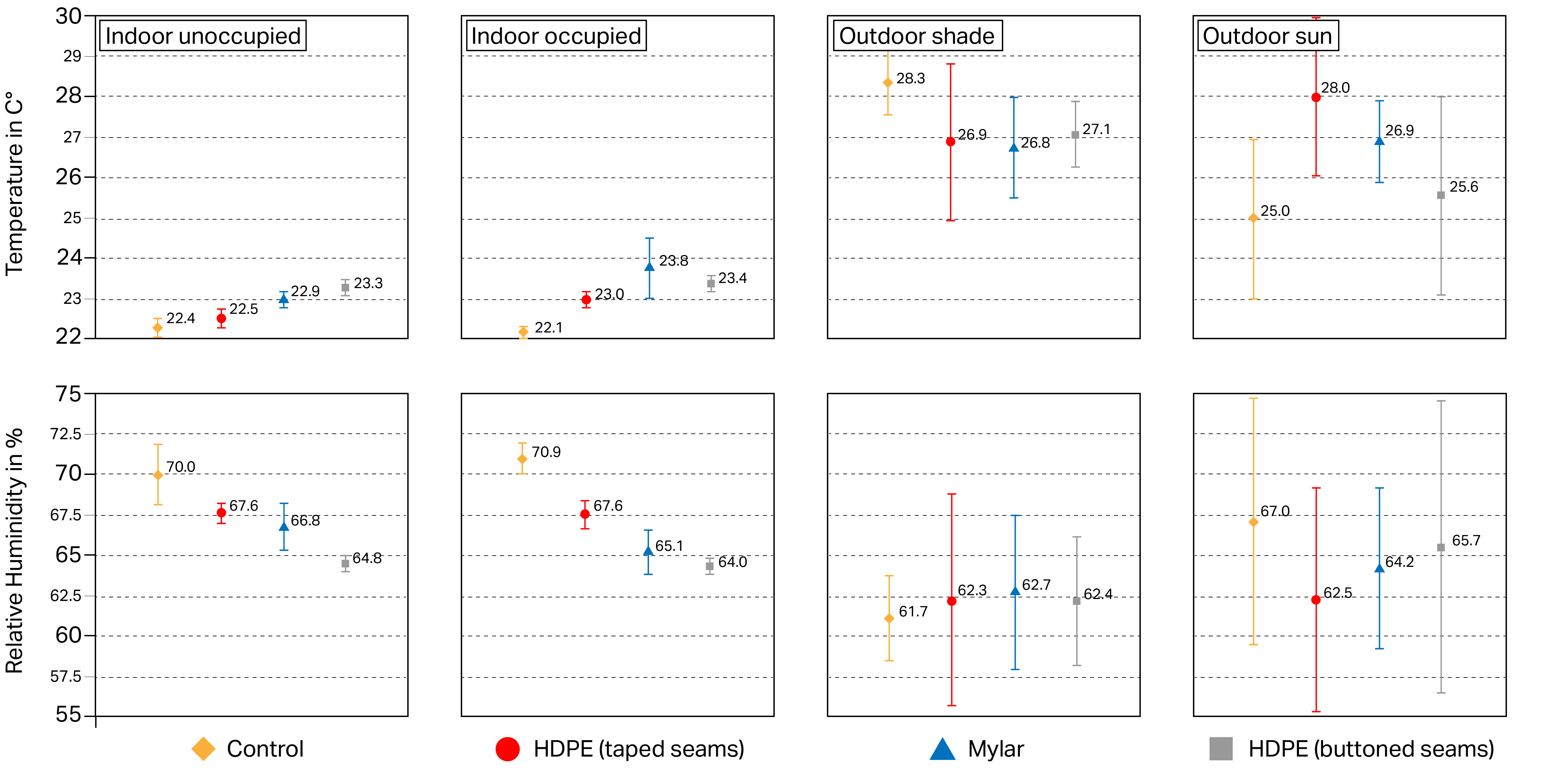
A custom-made patterning algorithm was developed to approximate component outlines using polygonal tessellation composed of 10 discrete units. The algorithm is inspired by quad-trees and employs units that can be systematically derived by cutting painter's tarps and Mylar blankets in their packaged state. This approach inverts traditional inflatable production, which is typically executed in a subtractive, material-intensive manner, by proposing an additive manufacturing process that generates almost no offcuts.
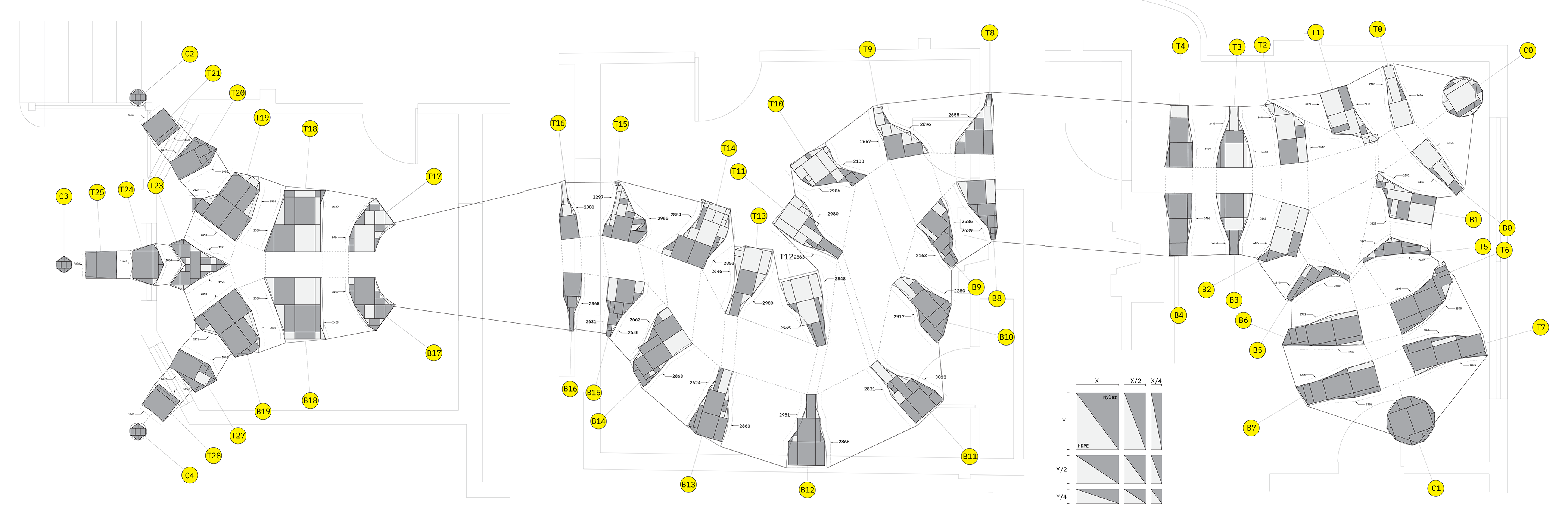

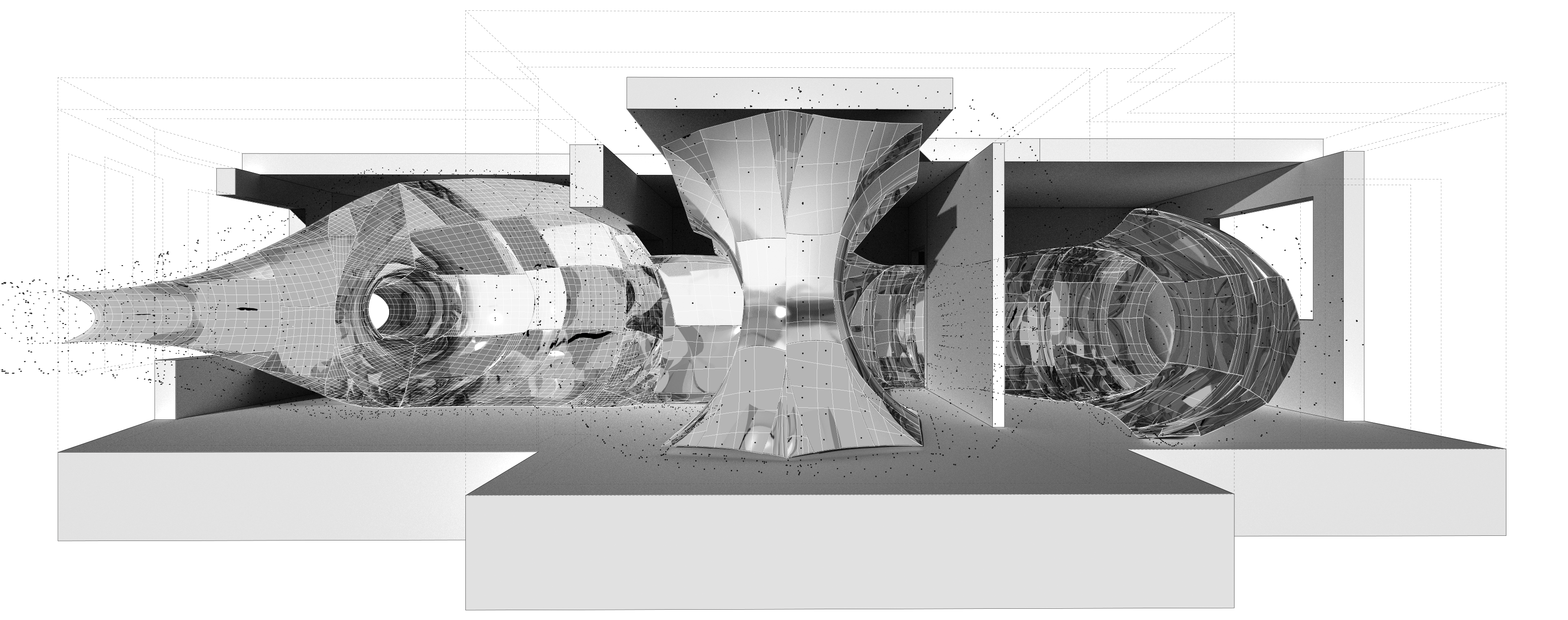
Building on the Unity AR-Foundation framework, findings from material experiments and patterning algorithms were integrated into an augmented reality (AR) app for mobile devices. This app features an ad-hoc, procedural modeling strategy with a simple and intuitive set of operations, including "Add Point," "Add Junction," and "Adjust Radius" and displays 2D instructions for patterning and fabrication.
![]()

During a two-day workshop, volunteer students utilized the AR app for modeling, patterning, and fabrication. Collectively, they created a full-scale demonstrator covering a 150 m² surface area, using only 3 kg of painting tarps/safety blankets and household tools. The previously unused and homogenized space was transformed into a temporary event and exhibition area, featuring varied spatial configurations and climatically differentiated zones.
![]()

Student Design Studies
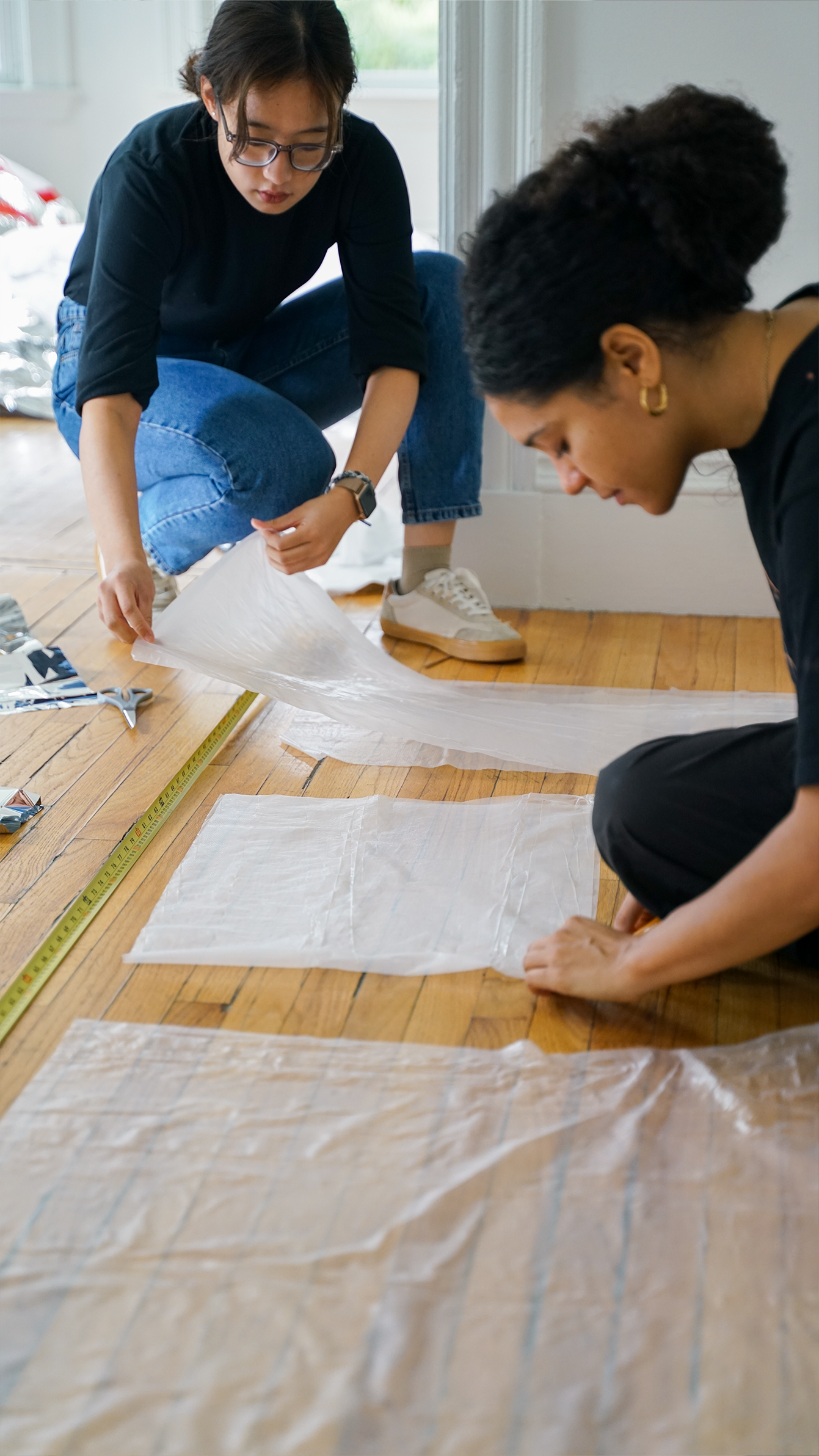

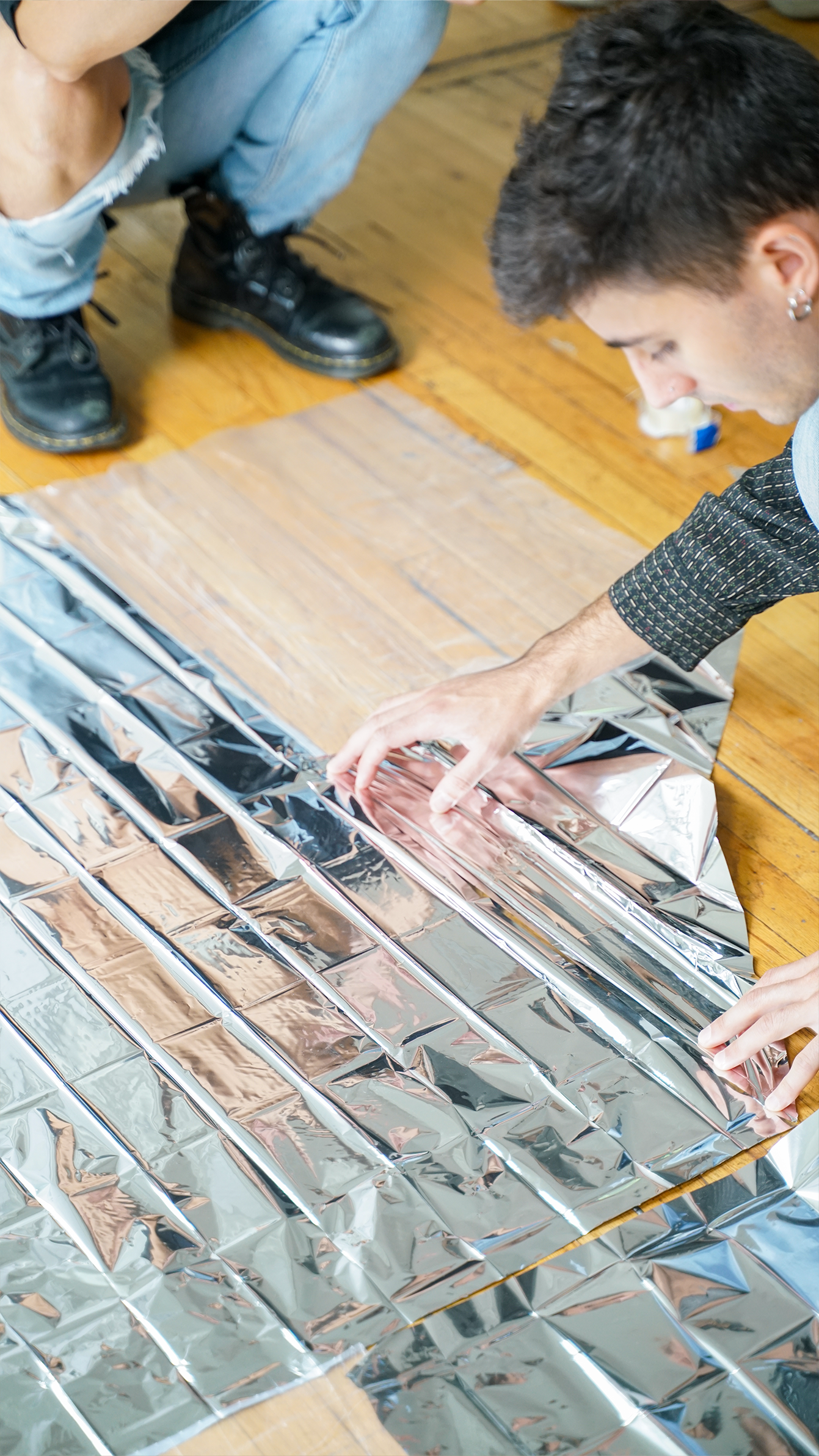


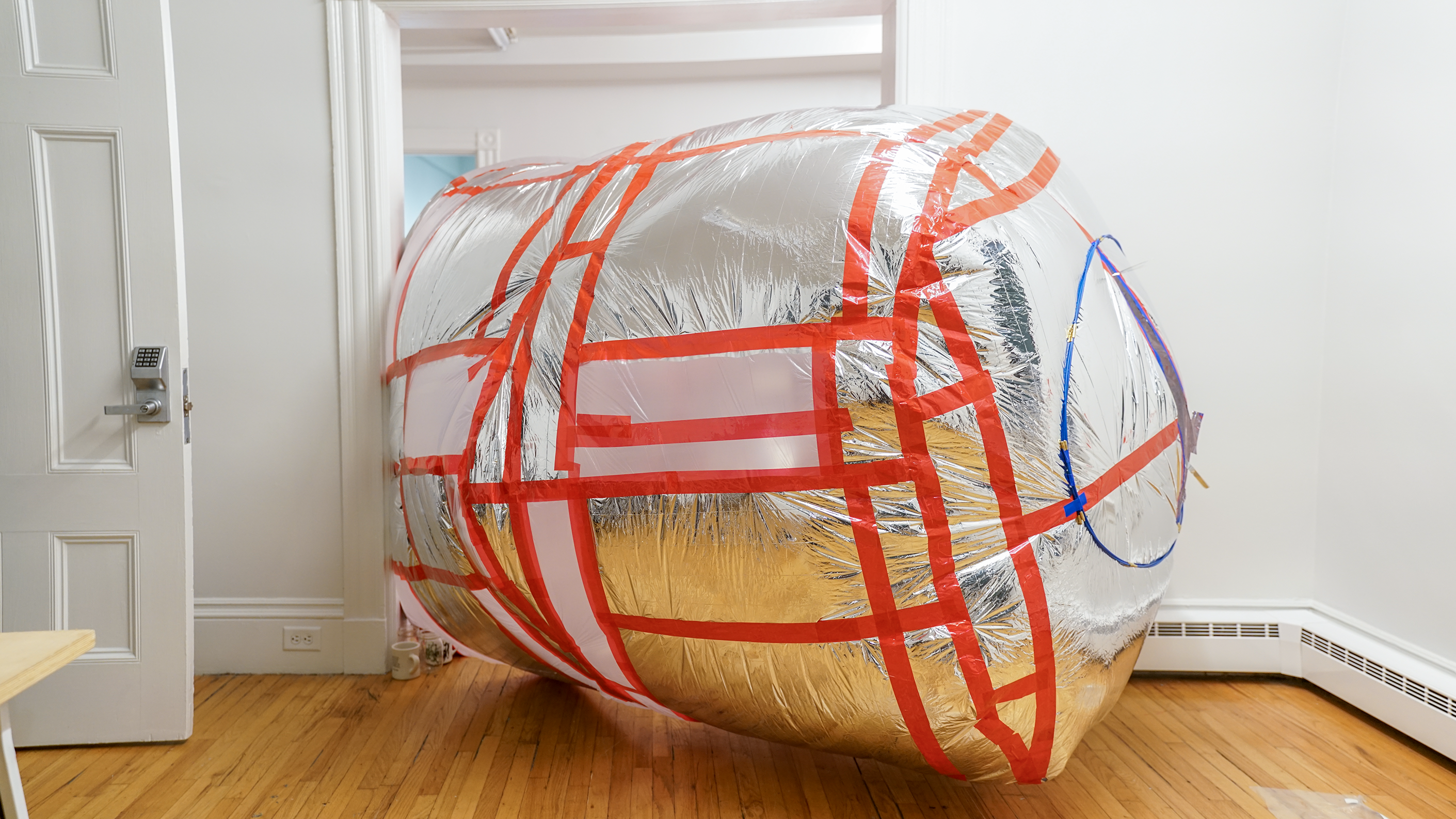
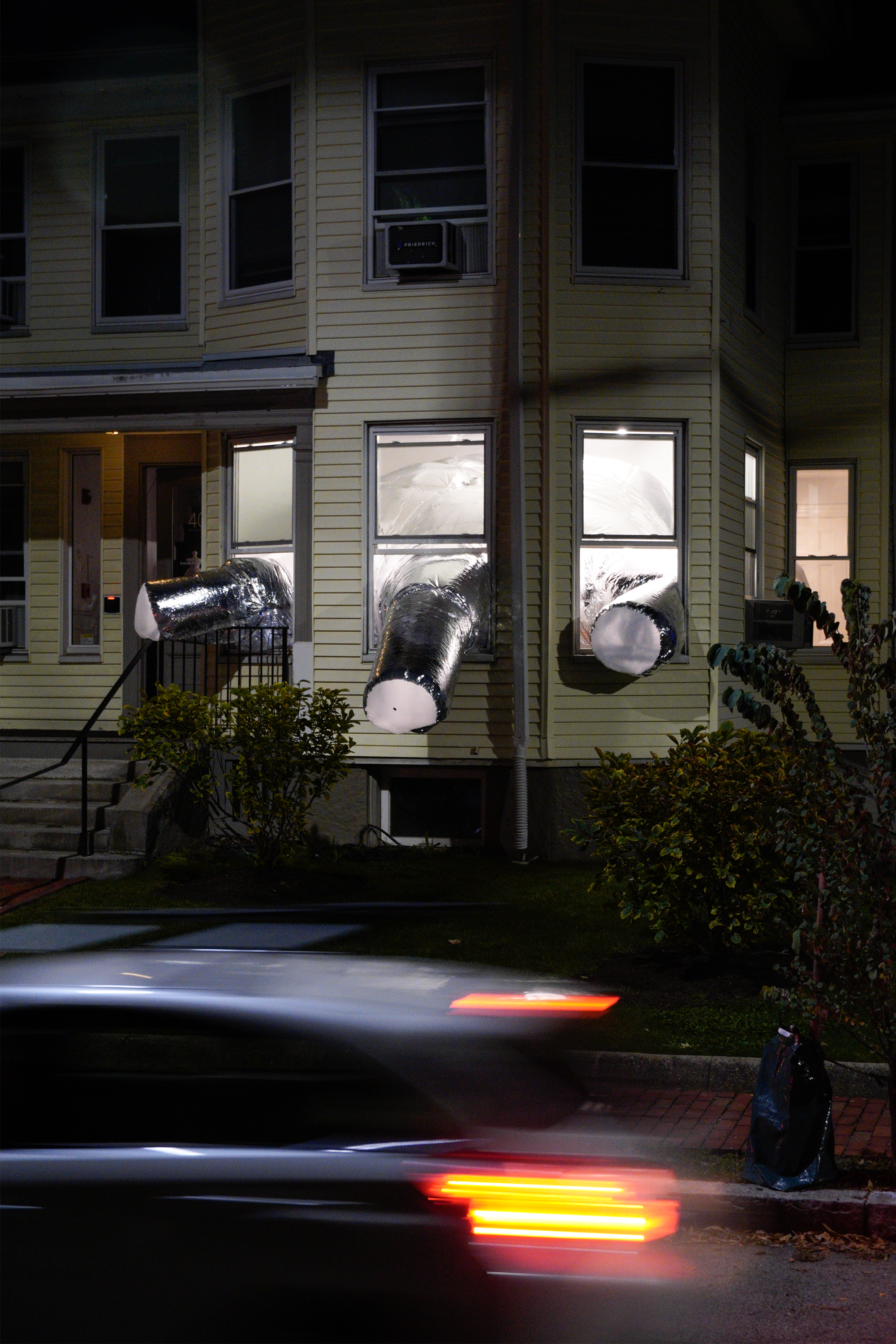



This project was conducted as part of the ITECH Master's Program at the University of Stuttgart, Germany. We extend our gratitude to our tutors and professors at the University of Stuttgart, the curatorial staff at the Harvard Graduate School of Design, and all workshop participants. This project was supported by the Builders-in-Residence Program at Autodesk in Boston.